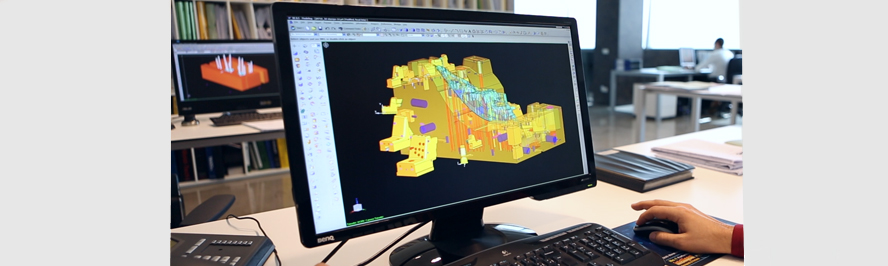
Over the years, SPM invested time, money and resources to make plastics mold design more and more evolved.
The construction of a product accompanies the creative intuition of the designer towards complete satisfaction consumer’s or final user’s tactile, aesthetic and functional requirements. It does not matter if the object is a simple component or if it has a defined unique use, or if it is a product that must meet many requirements that represent its success. Putting themselves in the customer’s shoes, so to speak, means at SPM being fully aware of this. It means not only converting an idea into a valued product on the market but above all supporting a customer in the evaluation of the materials to be used, proposing “non-conventional” and innovative solutions. Preparation of an “always open” project, on the cutting-edge of improvement at SPM means taking advantage of the research and development activities in order to design and produce a mould that represents an opportunity for innovation, adding value to the final product. Analysis and comparison of the data and experiences are activities that inform daily work in the engineering offices at SPM. The most advanced software and hardware technology available today is made available to engineers, who use it to give value to the high standards of professionalism established over decades in the company that enable them to take on the toughest challenges represented by global competition.
Within the mould design department for plastic materials, rubber and light alloys the technological evolution has been marked with growth and success. At the dawn of engineering design, there were great draftsmen, capable of hand-drawing full plans, and later, the advent of the first computers paved the way for the evolution of the field. Here, too, SPM was a pioneer. It was the first Italian customer in the moulds market for the Unigraphics software by McDonnell Douglas, which was later acquired by Siemens. The first computers required enormous investments, sustainable only with loans over several years; but this did not stop SPM from wanting to excel and innovate. The development of hardware, software, and in parallel, personnel training, has grown exponentially without interruption. SPM was among the first clients for Moldflow and other primary software houses for design, simulation and machining.
Today, SPM designs using NX, Catia, and ProE; FEM and the complete Insight MoldFlow software package that even allows for in-depth management of turbulent risers (which cannot be overlooked in thick pieces or with large changes in thickness), gravitational effects, thermodynamic conditioning of the moulds, and many other aspects that enable a very high level of analysis to be achieved.