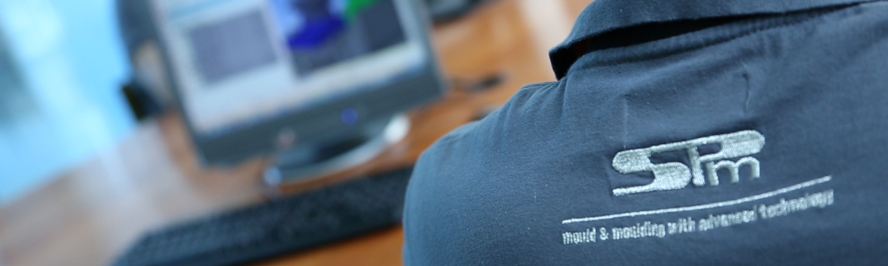
Understanding the potential in the relationship between a customer that has created a product and a supplier able to design and build the mould – as well as to the moulding – has been as natural as breathing at SPM for the last 40 years. In addition to reinforcing the company’s identity and highly specialized “mould and moulding” profile on the market, this policy has always driven the company’s technological evolution, enriching the extraordinary experience that makes SPM a top level partner for full product engineering and mould design. Expertise and experience are the assets SPM offers to support its customers, reaching levels of customer satisfaction that increase the value of the professional relationship established. All SPM’s tools and internal know-how are projected into the creation of something that has yet to exist!
SPM provides various services in the co-design and mould design, and can be described as follows:
- Digital reverse engineering without size limits, both on moulds and on products
- 3-D modelling of parts and moulds with the support of cutting-edge software: NX – CATIA – PRO-E
- FEM Analysis (Finite Element Method)
- Filling analysis using the complete Insight MoldFlow software package that even allows for in-depth management of turbulent risers (which cannot be overlooked in thick pieces or parts with big changes in thickness), gravitational effects, thermodynamic conditioning of the moulds, and many other aspects that lead to a very high standard of analysis.
The simulations performed are used to optimize filling of the mould from every point of view:
- Balancing filling allows the tonnage required to be minimised, therefore the size of the press and consequent production costs are also reduced
- Maximizing the surface quality of the part to give it a high-quality appearance
- Optimization of after-moulding deformation
- Optimization of production cycles thanks to the heat analysis and relative design of the cooling circuits.
Considering various factors:
- Number of cavities
- Type of injection
- Temperature
- Materials (using a database with highly detailed characteristics)
- Part geometry (shapes, thicknesses, etc.)
The result must always be compared with the original and must be interpreted correctly by highly qualified personnel for real application in the production department.